Lost time injury frequency rate (LTIFR)
Updated on 2023-08-29T12:00:41.907193Z
What is LTIFR?
Before describing the LTIFR, it is essential to know lost time injury. Lost time injury is defined as any injury sustained by an employee while on the job, and injury prevents the employee from performing the task at least by one day or during one shift.
In other words, if a person gets injured while at work and is not capable of carrying out his duties further, at least for the entire shift or the day, the time lost due to the injury is termed as lost time injury.
For reporting purposes, the companies report the lost time injury in one million man-hours of work. The number of lost-time injuries per million man-hours is Lost Time Injury Frequency Rate (LTIFR)
How is LTIFR calculated?
The formula for calculating the LTIFR is pretty simple and involves two sets of data only. One is the total number of lost-time injuries during the reporting period, and the total number of man-hours worked during the period. With basic these two data, the LTIFR of any firm or company can be calculated easily.
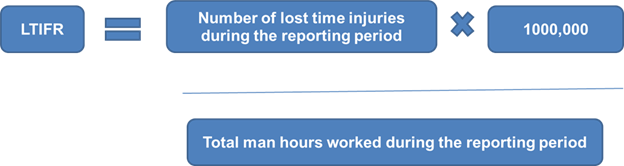
Copyright © 2021 Kalkine Media Pty Ltd.
Example - For any firm, the lost time injury is ten during the reporting period. Total man-hours for the firm are 3,000,000 hours. So, putting these two data in the above formula, we would get -
LTIFR = (10 X 1,000,000)/3,000,000
With a simple calculation, LTIFR is 3.33 for the above example.
The result reflects that the company has 3.33 lost time injuries for every one million man-hours worked. This figure could be used in making company reports and benchmark the company on the index of safety and work environment condition.
Summary
- LTIFR is a measure of how well an organisation is maintaining the safety at the workplace.
- An organisation with a lower LTIFR enjoys better goodwill in the industry and also tends to have more businesses than an organisation with higher LTIFR.
- With better training and safety policies, LTIFR can be kept in check and control.
FAQs:
How does LTIFR impact the organisation?
There are several industries that are prone to accidents and are classified as high-risk jobs. The mining and petroleum industry involves huge risk and chances of injury to the employees or damage to the environment is relatively high.
The government regulations demand a safer work environment for the people involved in hazardous jobs. If a company fails to provide one and reports, higher LTIFR continuously will attract legal actions and penalties.
Higher LTIFR would damage the goodwill of the organisation and may even cost business opportunities. A company with fairly high LTIFR is likely to get lesser business contracts from the government or other organisations, which puts the safety of employees at very high standards. They will refrain from doing business with such companies and may even blacklist them.
In one such incident, Arcelor Mittal, the European steel giant, blacklisted one of his contractors and 279 were given a strict warning for violating safety norms in 2016. The company was prompted to take this decision when its LTIFR increased from 0.48 in 2015 to 0.62 in 2016.
How to improve LTIFR?
With an increasing thrust on safety, organisations are putting in a great deal of hard work to keep their LTIFR low and promote a safe working culture. Mock drills and orientation are being done to keep the employees aware of the norms and regulations.
LTIFR can be improved at the workplace by following the below strategies:-
- Proper training of employees
The organisations need to invest more in employee induction and proper training on safety. Safety training and audits should be a continuous part of the company's operations. The employee's participation in such training should be ensured, and it must be taken care that each employee is well aligned with the company's safety policies.
- Regular Hazard Assessments
Hazard assessment is important and should be done before starting any operation. Employees with proper safety training should be given some kind of hazop card to identify and note any hazard they see on their job. The points in the hazop card should be maintained in a database and could be used in any other operations to avoid any hazard in advance.
In the mining and heavy industry, employees carry hazop card all the time, and whenever they encounter any hazard, they report it, and the superintendent or the manager makes sure that those hazards are worked upon to prevent any future accidents.
- Having a robust safety management system
Organisations should come up with a safety policy of their own and make it available to each and every employee. Then the organisation should set up a safety management system. Each hazard and incidents should be maintained in a database of the system.
If any lost time injury occurs, the detail of the incident or accident should also be maintained for future references. Employees should be encouraged to report the incidents and all the accidents, whether minor or major. This will lead to a vibrant database system that can be later on used as a case study for safety training and induction programs.
What are the limitations of using LTIFR?
Let us analyse two instances for this part. In one of the case, an employee with impeccable safety records slips and fell from the stairs and got a knee fractured. Although the accident was not fatal in nature, the fracture would result in lost time injury for over a week or longer.
In another event, a container dropped to the ground from a crane due to malfunction. The severity of this incident is really high and would cause immediate death or amputation of anyone who would have come in contact with the falling container. Luckily no one was on the ground at that time no accident occurred.
If we analyse the two situations, the severity was very low in the first case but resulted in LTIFR, while in the second case, no LTIFR was reported. The severity of the second incident is really high.
LTIFR is sensitive to injury management and reporting, not the part of severity, and does not reflect the true nature of the safety performances. LTIFR does not provide details of how well the incident was managed.