Acceptable Quality Level
Updated on 2023-08-29T11:54:07.649432Z
Acceptable Quality Level (AQL)
Acceptable Quality Level (AQL) indicates the acceptance limit for defects within a sample batch of products. It is an essential statistical metric for Companies following Six Sigma Quality Control norms. Since customers don’t expect any defects, thus it should ideally be zero, but zero defects are a rare reality. So, the Acceptable Quality level is generally determined using on production financial and safety risk levels. Other than this, defect acceptance depends on the type of Industry in which the business operates and customer needs.
Summary
- Acceptable Quality Level is the maximum per cent defective that can be considered satisfactory.
- It is a mutually decided, useful tool for accepting and rejecting a batch of goods manufactured and traded.
- The concept is widely used for Quality control in pharmaceutical, technology and various other industries.
Frequently Asked Questions (FAQs)
How is AQL useful?
Acceptance Quality Limit (AQL) concept was devised by Harold F. Dodge and has been modified and updated as per industry needs by other statisticians over time.
Today, AQL is a widely acknowledged practical approach for sampling during merchandise scrutiny. It considers deliberate risks for consumers and merchants. It gives a numerical reference to buyers and suppliers on number of defective products that are accepted under one single assessment.
The acceptable quality parameter is the quantity of tolerable defective products in a batch. Suppliers and consumers usually try to attain and set tolerable quality parameters. It is the maximum per cent defective that can be considered satisfactory. It is helpful for customers to decide on the acceptance/ rejection of any lot of goods.
Example: Lets’ consider a batch of 10,000 bags to be produced. Now Inspection of the set is to be undertaken when production is at Normal speed. Consider a producer whose average speed is 5000 bags in 10 days. Now AQL is expressed as a percntage for a given quantity of units produced. They are assuming the AQL to be 2 defects per 1000 bags. If there are overall 10 defects at an average production level, there is a high chance that the customer will reject the entire batch. Thus, reviewing the effectiveness of Quality control measures and reducing defects becomes essential. To avoid this from the start, production managers should ensure that less than 2 defective pieces are found in any batch of 1000 bags manufactured in a go.
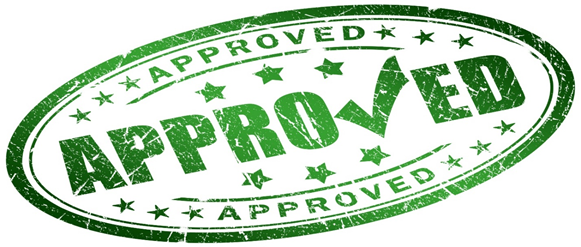
Image Source: © Arcady31 | Megapixl.com
What are the factors dictating AQL?
AQL is the level of defect agreed by the buyer and supplier based on the importance of the product. Say in the case of high-cost items, AQL should be at the lowest level. It shall, in turn, result in cost control. Thus, it is the reason why various factors like the following are used to determine AQL.
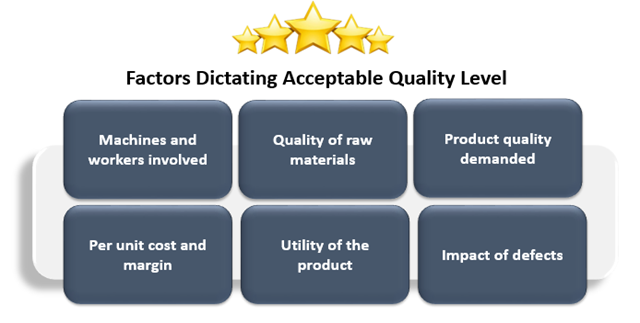
Copyright © 2021 Kalkine Media
Other broad Industrial factors are also considered along with any other factors that affect Quality. Factors like potential cost of calling back inventory after booking sales or cost of sales return is also an essential factor for determining AQL. Thus, AQL is approved by the buyer in consultation with the supplier based on the significance of the product.
For example, the AQL for a batch of bags can be 2 per 1,000, while it cannot be this high for a batch of emergency use medicines or high-value items like microprocessors, capital goods or currency notes.
How does the type of defect define AQL?
Clients logically want to have zero-defect products or services. Thus for them, the ideal acceptable defect level is null. This is based on the harm they can cause to the customers’ quality needs. But not all defects rank the same. Defects are therefore categorized as below to define AQL-
- Critical defects: if these are accepted may harm users. Such defects are intolerable. Therefore, the definition of Critical defects becomes 0% of AQL.
- Major defaults: these are defects intolerable to customers. These can result in deal failure.
- Minor Errors: such Flaws do not impact the utility of the or envisioned purpose of any product. Such faults differ from specified standards. They are not easily detectable, and customers may buy such products.
How is it determined using AQL Tables?
AQL Tables are an easy way to determine AQL. They are commonly used and accepted method for inspection across industries. AQL Tables are also called ANSI Tables. The following 3 parameters are needed to make up an AQL Table-
- The Lot Size- it is the numbers of products grouped together as a lot/ batch.
- Inspection Level- There are different levels set as inspection levels depending on sampling needs.
- AQL limits- the level appropriate as per market or Industry of operation.
Quality control departments or Quality Auditors use such predefined AQL Tables or excel charts for sampling. Sampling is done to inspect and improve manufacturing Quality or providing Quality certifications.
Can AQL ensure zero defects?
Now one may think that a 100% inspection of all goods would give 100% surety that products are fit for use. If it is a matter of low volumes, this is reasonable. But, as order quantities go up, inspecting each unit produced becomes less feasible. It becomes time-consuming and costly.
AQL is a proven statistical model that utilizes the theory of sampling for Quality Control. It has been operatively used across businesses for years. However, it does not promise a defect-free inspection. It is not planned to confirm zero defects. Instead, it helps determine a tolerable limit for defects. It is just a risk management tool.
As per the ISO 2859 standard, which defines AQL -
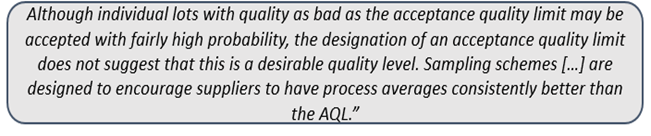