Oil Drilling
Updated on 2023-08-29T12:00:35.895513Z
Oil drilling is the process of drilling a circular cross-sectional hole from the surface of the Earth to reservoirs, where the hydrocarbons are deposited. The process helps to extract the deposited hydrocarbons from the subsurface formations to the surface. This is the fundamental process to extract hydrocarbons from the subsurface. The process involves huge machinery, including drill bits, pumps, motors, drill pipes, etc., assembled into a single platform commonly known as a drilling rig.
Types of Drilling:
Based on drilling a well, the drilling can be classified into two broader categories: Onshore and Offshore drilling. To understand the basic difference between both, let us have a look below:
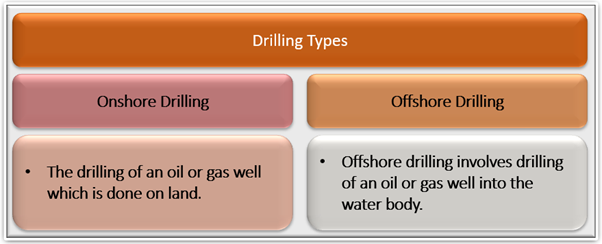
Copyright © 2021 Kalkine Media Pty Ltd
Onshore Drilling:
The drilling of an oil or gas well that is done on land is known as Onshore drilling. The road transportation network transports the drilling rigs, and rigs are placed on the ground. Mobile rigs or truck-mounted rigs are used also used in this type of drilling. The operating expense of onshore drilling is relatively less than offshore drilling as it doesn't incur any helicopter transportation costs of crews, additional shipping costs for living supplies, and food. The infrastructure to drill an onshore well can be constructed in a lesser time compared to an offshore structure.
Offshore Drilling:
Offshore drilling involves drilling of an oil or gas well into the water body, i.e., into the oceans. Offshore rigs like floating, drillship, semi-submersible, or Jack-up rigs are used in this type of drilling. The transportation of rig components is primarily done through mega-ships and carriers. The components are assembled at the location of the drilling, which requires additional time for the drilling to proceed. The operating cost of offshore drilling is much more than that of onshore drilling. Also, the operations are riskier than onshore operations.
The Drilling Process:
The complete drilling process can be sub-divided into six major steps. Let us try to glance at each step, in brief, to understand the complete drilling process.
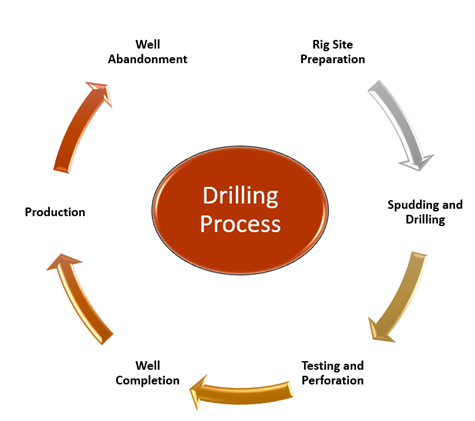
Copyright © 2021 Kalkine Media Pty Ltd
- Rig Site Preparation: The is the foremost step for drilling an oil or gas well. Before the start of drilling, the rig site and infrastructure related to the drilling is being prepared. For example, access roads and drilling pad are prepared, safety procedures and noise barriers are carefully planned in accordance with local and state government. Arrangements for electricity, water disposal, and mud pits are undertaken. Groundwater table confirmation to avoid water contamination is taken care of.
- Spudding and Drilling: After all the necessary arrangements have been made and proper inspection of every piece of equipment is completed. The well is spudded with the help of rotary drilling operations.
After reaching the first casing depth, i.e., surface hole, the well is cased with the help of a steel pipe known as casing. The steel casing is then cemented with cement to avoid the collapse of the wellbore allowing the company to proceed with further drilling. When the cement gets hard enough, the drilling process is resumed to drill up to the next casing depth. The depth of the next casing point, i.e., Intermediate Casing, depends on various factors like fracture gradient of formations to be drilled, mud weight, location of any lost circulation zones, and high-pressure zones, etc.
Once the final intermediate casing string is run and cemented, the drilling process is again resumed to reach the wellbore's final depth. After reaching the final depth, also known as total depth (TD), various logging tools are introduced into the wellbore to measure certain reservoir properties. Afterwards, cementation of production casing string or production liner is being undertaken.
- Testing and Perforation: After reaching the TD and before starting any hydrocarbon production, the well undergoes various types of tests to ensure that the pipe is impermeable. If the well passes through multiple types of testing, it is perforated with the help of perforating guns. The guns fire into the subsurface formation, creating holes that connect the rock holding hydrocarbons and the wellhead.
- Well Completion: After completion of the perforation, the well is introduced with a high-pressure fracking fluid containing 99.5 per cent water and sand and 0.5 per cent chemicals to keep the thin fractures open and permeable so that the hydrocarbons can flow through the fractures easily.
- Production: Upon well completion, hydrocarbons start flowing up through the wellbore, and production begins. The well continues to flow till the reservoir pressure drops significantly. Upon pressure drop, steams or gas are injected into the wellbore to again increase the reservoir's pressure and increase the production rate.
- Well Abandonment: After recovering all the hydrocarbon from the wellbore, the well is plugged and abandoned, and the land is kept for restoration.
Drilling Types based on Hydraulic Heads:
Generally, in the oil and gas industry, two major types of drilling approaches of drilling are carried out based on the hydraulic heads while drilling. One is known as underbalanced drilling and the other is known as over-balanced drilling. Let us try to understand these in brief.
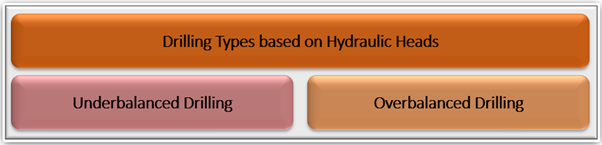
Copyright © 2021 Kalkine Media Pty Ltd
- Underbalanced Drilling: Underbalanced Drilling of UBD is a condition while drilling where the wellbore pressure is kept lower than that of the formation fluid pressure. As the drilling goes on, formation fluids start entering the borehole because the wellbore exposed formations exert pressure on drilling mud and start entering into the wellbore. UBD leads to an increase in the drilling rate.
- Overbalanced Drilling: Overbalanced Drilling or OBD is a type of drilling where the pressure inside the borehole is kept higher than that of formation pressure. The higher pressure is maintained with the help of pumps. While maintaining the pressure, the limit of formation breakdown is kept in mind to avoid lost circulation. Also, excess overpressure can reduce the drilling rate by slowing the removal of drill cutting under the bit.